Due Diligence No Matter the Job
All customer projects are important. We conduct up-front due diligence to understand the intricacies of the assembly, critical in-process functional characteristics monitoring, cosmetic expectations, packaging requirements and quality history if available. These inputs are critical and assist us in structuring our manufacturing process. With this detail we can quote the project so that customers will be absolutely satisfied. We always take the time upfront to understand what it’s going to take to deliver the project properly.
Error Proofing
Error proofing the process is critical as it’s the key to ensuring that the manufacturing process doesn’t allow a defect to pass thru to the customer. At Performance Assembly Solutions, we use a variety of different methodologies to error proof the manufacturing process. These methodologies may be used solely or in combination depending on the project. The general logic is that we focus on creating a sequential verification process control. Sequential verification ensures every manufacturing process step is correct. It only allows the technician to continue to the next process step if the prior step was done correctly. Inputs that we employ for sequential verification control include:
- Electromechanical part interlocks
- Automated fastener socket trays
- Leak-test controller outputs
- Weight verification
- In process bar code scanning
- Automated part bin systems
- Laser part detection
- Air-gaging measurement outputs
- Part present switches
- DC tooling outputs
- Vision systems
- Etc.
Calibration
At Performance Assembly Solutions, we invest in the tooling and equipment to do the job right the first time. This equipment requires periodic calibration to verify repeatable output. Repeatability is necessary to give our customers comfort that our manufacturing process is robust and will produce the same quality product every time. Our calibration schedules are well defined and monitored to ensure the frequency schedule established is adhered to.
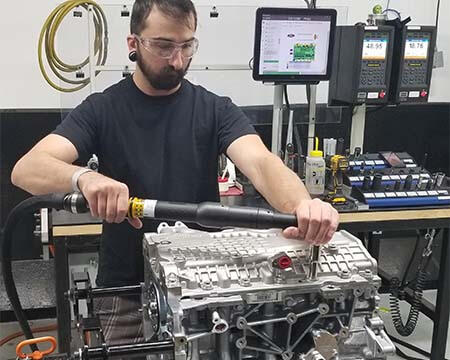
Technician Training
The effort we do up-front to design and invest in a robust error-proofed process is a major part of ensuring we deliver quality finished goods. Verifying our technicians are properly trained and following the defined procedures is equally critical We recruit experienced technicians and have established partnerships with industry recognized trade schools to place graduates. All technicians undergo thorough job specific training with an assigned trainer, ensuring they understand the workflow process and the equipment control. When a technician can demonstrate their ability to train their trainer, we’re certain they are ready to perform the job.
Layered Audits & Floor Auditors
Day to day process monitoring is a key element of our quality system. This “fresh eyes” approach compliments our process design, calibration and technician process outputs. Layered audits are conducted by the management team as an extra layer of process verification. These audits ensure we do what we say we do which produce superior results for our customers.
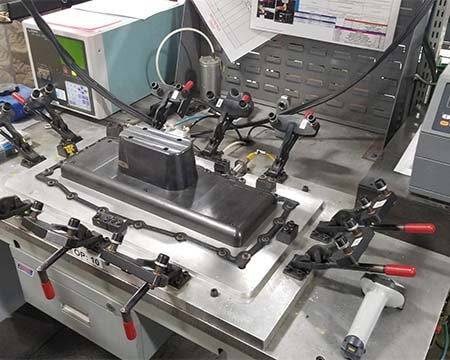
Performance Assembly Solutions
Shipping and Receiving
Phone: (734) 466- 6376
william.clendenin@performanceas.com
Business Development
313-319-4042
chris.zucker@performanceas.com
Address:
